Rapid Prototype Molding: Transforming Ideas into Reality
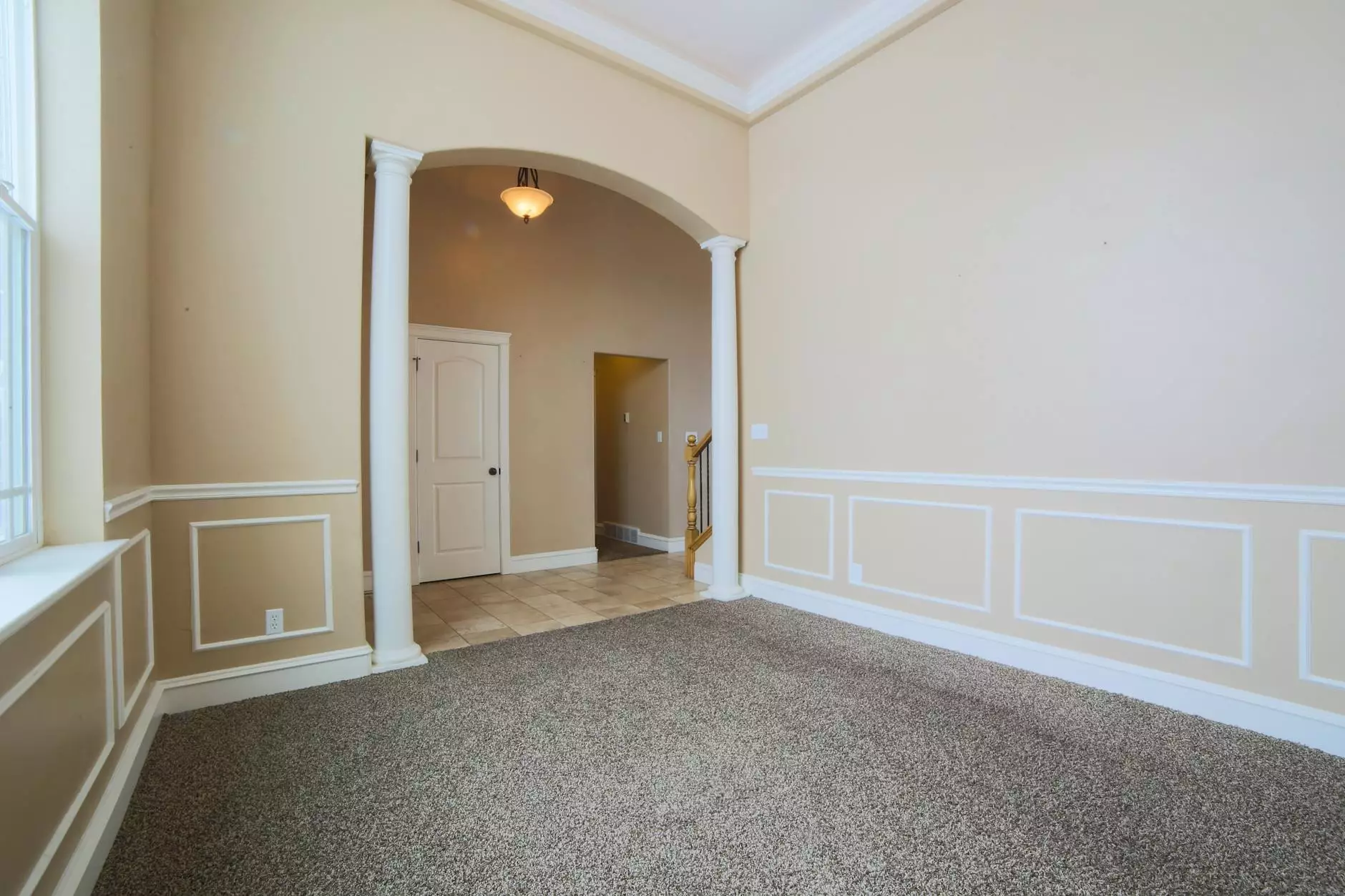
In the fast-evolving world of manufacturing, the emphasis on speed and efficiency has never been greater. Rapid prototype molding emerges as a game-changing technique that facilitates acute precision and innovative designs in various industries. As businesses strive to stay ahead in competitive markets, understanding the intricacies and advantages of rapid prototyping is crucial.
Understanding Rapid Prototype Molding
Rapid prototype molding is a revolutionary process that allows manufacturers to create functional prototypes quickly. This technique supports visual and functional verification of designs, ensuring that potential issues are addressed before progressing to full-scale production. By utilizing this method, companies can save both time and resources and promote effective product development cycles.
What is Rapid Prototype Molding?
At its core, rapid prototype molding refers to the use of 3D printing and other advanced molding techniques to create prototypes of products in a significantly reduced timeframe. Instead of traditional manufacturing methods, which can take weeks or months, rapid prototyping streamlines the process to just a few days. This enables manufacturers to bring their ideas to market faster and more efficiently.
Benefits of Rapid Prototype Molding
The advantages of rapid prototype molding extend beyond mere speed. Here are some key benefits that make it an essential process for modern businesses:
- Fast Turnaround: Rapid prototyping significantly reduces the time from concept to prototype. This speed allows for quicker testing and validation of designs.
- Cost Efficiency: By minimizing the need for extensive resources and labor, companies can save on costs related to material wastage and labor during the prototyping phase.
- Design Flexibility: Modifications can be made swiftly and inexpensively, enabling designers to explore various iterations without incurring high costs.
- Enhanced Communication: Having a tangible prototype aids in better communication among stakeholders, ensuring that everyone has a clear understanding of the product.
- Improved Quality: Early detection of design flaws reduces the risk of costly errors during mass production, leading to higher quality final products.
Techniques in Rapid Prototype Molding
Various techniques are utilized in rapid prototype molding, each with its unique strengths. Understanding these can help businesses choose the right method for their needs:
1. 3D Printing
3D printing, or additive manufacturing, is perhaps the most well-known technique in rapid prototyping. This process involves creating a three-dimensional object by layering materials based on digital models. It allows for intricate designs and can accommodate various materials, including plastics and metals.
2. CNC Machining
CNC (Computer Numerical Control) machining involves the use of software to control machine tools. It's an excellent process for producing highly accurate parts quickly and is applicable to a wide range of materials.
3. Injection Molding
While traditionally slower, advancements in injection molding methods have enabled some rapid prototyping capabilities. This technique is particularly useful for producing plastic parts and is often employed when high volumes are anticipated in full production runs.
4. Foam Molding
This method utilizes foam to create prototypes quickly, especially in automotive and aerospace sectors. It allows for lightweight, yet durable prototypes that are perfect for testing aerodynamics and design.
The Role of Rapid Prototype Molding in Metal Fabrication
When it comes to metal fabricators, rapid prototype molding plays a vital role in developing components that require precision engineering. Here’s how it integrates with the metal fabrication process:
1. Prototyping Complex Designs
For metal fabricators, creating prototypes of intricate designs can be a challenge. Rapid prototyping techniques enable them to experiment with complex geometries that would be difficult or impossible to produce using traditional methods.
2. Testing Functionality and Fit
Before committing to large-scale production, fabricators can utilize rapid prototyping to test the functionality and fit of metal components. This helps ensure that any issues are rectified early in the production phase, minimizing costly reworks.
3. Material Testing
With different metals behaving uniquely under various conditions, rapid prototyping allows fabricators to test different materials under realistic conditions to understand better their mechanical properties and suitability for the intended application.
Challenges Faced in Rapid Prototype Molding
While the benefits of rapid prototype molding are compelling, challenges still exist. Understanding these can help businesses navigate potential pitfalls:
- Material Limitations: Not all materials are suitable for rapid prototyping, and in some cases, the choice of material may limit functionality.
- Surface Finish: Prototypes often require post-processing to achieve a desirable finish, which can add time and cost to the project.
- Scale Limitations: Some rapid prototyping techniques may not be ideal for producing large-scale components, necessitating a transition to traditional methods for mass production.
The Future of Rapid Prototype Molding
The future of rapid prototype molding looks promising, with ongoing advancements in technology. Emerging technologies such as generative design, artificial intelligence, and improved materials are set to transform the landscape of rapid prototyping, making it even more integral to manufacturing processes.
1. Generative Design
This innovative design process uses algorithms to explore all possible combinations of a solution, resulting in enhanced performance and reduced material waste. The integration of generative design with rapid prototyping could lead to breakthrough innovations.
2. Advanced Materials
As material science progresses, designers will have access to new materials with unique properties specifically engineered for rapid prototyping, expanding the possibilities of what can be achieved.
3. Integrating AI and Machine Learning
With AI and machine learning, manufacturers can refine their prototyping processes, predict outcomes, and automate certain stages, leading to incredible efficiencies and accuracy improvements.
Conclusion
In conclusion, rapid prototype molding is revolutionizing the landscape of manufacturing and metal fabrication. Its ability to produce high-quality prototypes quickly and cost-effectively drives innovation and efficiency across industries. As technology advances, the potential of rapid prototyping will only grow, offering endless possibilities for businesses aiming to lead in their respective sectors.
For businesses looking to enhance their prototyping efforts, embracing modern techniques such as those found at deepmould.net can be an essential step towards achieving superior product development and manufacturing excellence.